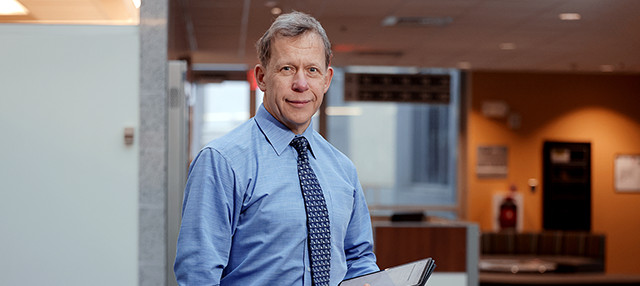
A simple, scalable method using light to 3D print helical nanostructures
New process can accelerate the production of complex materials needed to advance photonics technologies
New process can accelerate the production of complex materials needed to advance photonics technologies
Written by Patricia DeLacey.
A new fabrication process for helical metal nanoparticles provides a simpler, cheaper way to rapidly produce a material essential for biomedical and optical devices, according to a study by University of Michigan researchers.
“One of our motivators is to drastically simplify manufacturing of complex materials that represent bottlenecks in many current technologies,” said Nicholas Kotov, the Irving Langmuir Distinguished University Professor of Chemical Sciences and Engineering at U-M and co-corresponding author of the study, published in Proceedings of the National Academy of Sciences.
Chiral surfaces—meaning the surface lacks mirror symmetry (e.g., a left and right hand)—that have the ability to bend light at the nanoscale are in high demand. The new study demonstrates a way to make them by 3D-printing “forests” of nanoscale helices. Aligning the helices’ axes with a light beam creates strong optical rotation, enabling chirality to be harnessed in health and information technologies, for which chirality is common.
Chiral surfaces from plasmonic metals are even more desirable because they can produce a large family of very sensitive biodetectors. For example, they can detect specific biomolecules—produced by dangerous drug-resistant bacteria, mutated proteins or DNA—which can aid the development of targeted therapeutics. These materials also offer potential to advance information technologies, creating larger data storage capacities and faster processing speeds by harnessing the interaction of light with electronic systems (i.e., fiber optic cables).
Although these special 3D-structured surfaces from stand-up helices are much needed, the traditional methods to make them are complex, expensive and create a lot of waste.
Most commonly these materials are made using highly specialized hardware—such as two-photon 3D lithography or ion/electron beam-induced deposition—only available in a few high-end facilities. Although accurate, these methods involve time-consuming, multi-step processing at low pressure or high temperature conditions.
3D printing has been suggested as an alternative, but existing 3D printing technologies do not allow nanoscale resolution. As a solution, the U-M research team developed a method that uses helical light beams to produce nanoscale helices with specific handedness and pitch.
“Centimeter-scale chiral plasmonic surfaces can be produced within minutes using inexpensive medium-power lasers. It was amazing to see how fast these helical forests grow,” said Kotov.
The 3D printing of helical structures by helical light is based on the light-to-matter chirality transfer discovered at U-M about 10 years ago.
Single-step, mask-free, direct-write printing from aqueous solutions of silver salt provides an alternative to nanolithography while advancing 3D additive manufacturing. The processing simplicity, high polarization rotation and fine spatial resolution of light- driven printing of helices from metal will greatly accelerate the preparation of complex nanoscale architecture for the next generation of optical chips.
Kotov is also the Joseph B. and Florence V. Cejka Professor of Engineering and a professor of macromolecular science and engineering.
This work was conducted at the Lurie Nanofabrication Facility and the Michigan Center for Materials Characterization.
This work was funded by the U.S. Department of Defense Vannevar Bush Faculty Fellowship for Nicholas Kotov (ONR N000141812876), the U.S. Office of Naval Research (HQ00342010033; N00014-20-1-2479), the U.S. Air Force Office for Scientific Research (AFOSR FA9550-20-1-0265), and the National Science Foundation (CMMI- 1463474; NSF 2243104; CHE-1807676)
Additional University of Michigan co-authors: Connor McGlothin, Minjeong Cha, Zechariah J. Pfaffenberger, Emine Sumeyra Turali Emre, Wonjin Choi, Sanghoon Kim, and Julie S. Biteen.